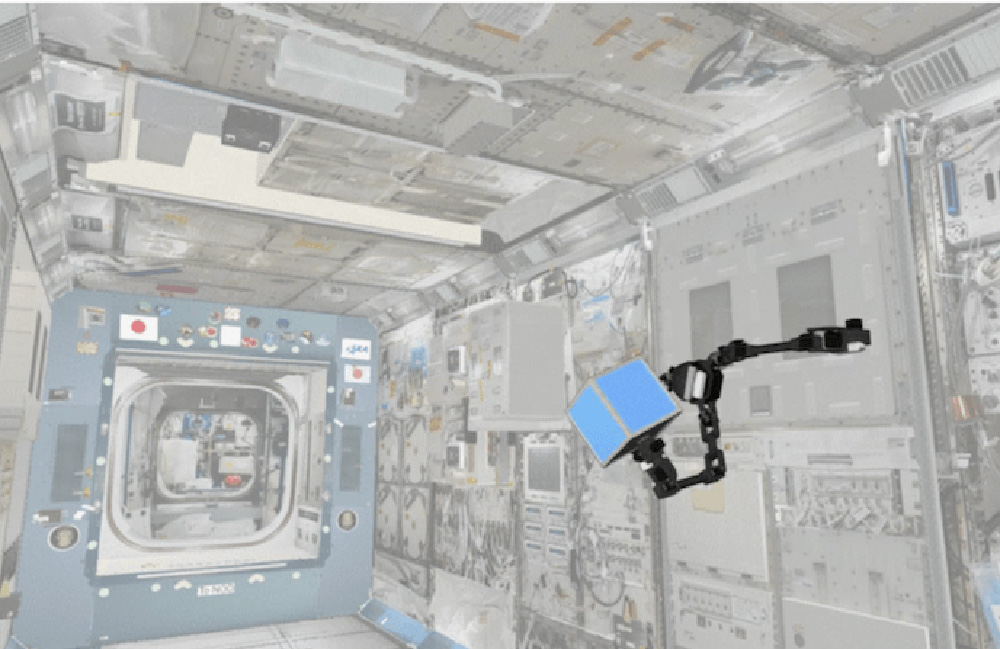
MoveIt Pro was evaluated by JAXA as the planning and control backbone for PORTRS. | Source: PickNik Robotics
PickNik Inc. recently partnered with the Japan Aerospace Exploration Agency, or JAXA, to change how the International Space Station handles cargo and equipment. The project is part of JAXA’s Payload Organization and Transportation Robotic System (PORTRS) initiative.
The goal was to demonstrate a complex, multi-armed robotic system capable of performing manipulation tasks in microgravity. These could include anything from crawling, payload swapping, to handling soft, flexible cargo transfer bags. These mundane tasks are not the most valuable use of an astronaut’s time, Dave Coleman, founder and chief product officer of PickNik, told The Robot Report.
“Some of the examples they’ve cited are just routine maintenance tasks,” he said. “A lot of these astronauts have Ph.D.s, or they’re super accomplished fighter pilots, and you’re asking them to wipe down air vents and clean surfaces, or to move cargo around when they have to resupply.”
Every hour of an astronaut’s time in space can cost as much as $200,000, Coleman noted. “There are so many other expenses that go into training and prepping and launching, and then there’s the cost of the life-support systems,” he continued. “So anything you can do to augment astronauts with robots has a huge ROI.”
“There’s a case where an astronaut’s sock floated into an air vent and was clogging it, which is bad for the life-support system,” Coleman said. “So you could perceivably have a robot go and do a pick-and-place task and clear that out. There are lots and lots of use cases that both the NASA and the JAXA side have been looking at for having a robot assisting astronauts.”
With the latest demonstration, JAXA hoped to prove that its system could meet the demands of real-world, high-stakes space operations with greater speed, robustness, and readiness for practical deployment.
PickNik helps JAXA build robots for low gravity
While there are more similarities than differences in terrestrial and space use cases, many of the specific capabilities for robots in space are in the firmware layer. While PickNik doesn’t get involved in this area, the Boulder, Colo.-based company still had to create a system using MoveIt Pro that could operate in zero gravity.
Coleman said that terrestrial robots, like a typical collaborative robot arm, take gravity into account in their control systems. Shifting to zero gravity means making a low-level change in how you tune your controls, he explained. Once you account for that difference, things run similarly.
JAXA’s robot has four arms and a non-fixed, reconfigurable base. With no gravity, the robot can use any surface to stabilize itself. The Japanese space agency‘s robot can crawl around a spacecraft, like a spider. It can use any of its four arms to stabilize itself, typically on the rails that the ISS is already has for human astronauts to use.
“You grab onto this metal railing, and depending on which appendage is attached, the fixture point changes,” explained Coleman. “So all the math behind it transforms, and the inverse kinematics, all of those things have to be very dynamic and change based on where your legs are.”
MoveIt Pro enables quick iteration
While JAXA has tested a four-armed version of its robot, the final flight model will use a three-legged configuration. Modularity and adaptable control are even more critical.
“A lot of robotics companies, they can move fast and make some assumptions and take shortcuts by hard-coding the number of joints,” Coleman said. “We’ve taken the harder approach, where all of our control systems and control algorithms automatically adjust to how many degrees of freedom or how many appendages you have. That’s really powerful, and that enables rapid prototyping.”
Designing robots for space also means taking in additional safety concerns.
“You have to do a lot more validation and verification because if a robot punches a hole into your space station, that’s really bad for all the humans living there,” Coleman said. “It’s a very brittle system up there, and so there’s a lot more safety checks on the amount of force being exerted and the speed at which each joint can run.”
PickNik also ensured that human-in-the loop functionality was strong in JAXA’s system. Real-time teleoperation isn’t possible because of latency between mission control and the ISS, and the space agencies prefer to review all commands rather than rely on full autonomy, said Coleman.
Coleman discusses PickNik’s future plans in space robotics
PickNik is in talks with other U.S.-based customers that want to create similar mobile manipulators. Coleman said working with JAXA has helped the company refine its approach.
In addition, PickNik has added features around supporting multiple arms and dynamically switching between which ones are active and which ones are fixed. It has been working with JAXA to mature the technology.
“We are, admittedly, still a bit more of an experimental program for JAXA,” Coleman acknowledged. “I think we’re going to be more in their second-generation application.”
But PickNik has many other space robotics projects on the horizon. For example, it is working with the U.S. Space Force on satellite capture and grappling projects. It has also been working with NASA on a number of lunar surface applications.
NASA faces uncertainty as JAXA moves quickly
With the current administration’s plans to cut 24% of NASA’s funding and eliminate 41 science projects, the future of U.S. space robotics is in flux. Despite these challenges, PickNik plans to continue pursuing space applications.
“We’ve always had dual-use, so lots of non-space applications,” Coleman said. “That’s the bread and butter of our business. We’re making a lot of progress with some exciting customers in the space industry. It moves slowly, and there are a lot of fits and starts.”
“We’re trying to play the long game of being sustainable through non-space applications while waiting for the right timing, which can take multiple years,” he added.
There are also other changing dynamics in the industry. Coleman said that with SpaceX’s Starship maturing and hopefully having its first real missions, the cost of launching commercial payloads could drop. This would make it more cost-effective to put satellites into orbit, making satellite servicing less of a priority.
While space robotics typically moves slowly, Coleman noted that JAXA has moved quickly with PORTRS.
“One thing that’s really cool about it is just how fast they’re moving,” he said. “Their launch timeline is way faster than most programs.”
The post JAXA tests PickNik’s MoveIt Pro software in multi-armed robotic system for the ISS appeared first on The Robot Report.